- Trophées de l’Innovation et de la Transformation Numérique 2023
- INDUSTRIE - Renault : son métavers industriel, replica du monde physique piloté en temps réel
- BANQUE - BNP Paribas : du SI à l’innovation digitale, l’IT du Groupe au point de convergence
- SERVICE PUBLIC - Le SDIS 43 mise sur l’hyperconvergé pour moderniser son SI
- SANTE - Inria : le jumeau numérique, virage décisif pour la santé
- DIGITAL RETAIL - Carrefour : innover pour devenir une Digital Retail Company
- SPECTACLES - LDLC Arena, l’espace de spectacle du futur
- SPORT AUGMENTÉ - Fitness Park réinvente le sport, connecté et gamifié
- FORMATION - Excelia associe innovations pédagogiques et numériques
La “Renaulution industrielle” du XXIe siècle est en marche ! Elle s’appuie sur un métavers industriel, rencontre entre les mondes physique et virtuel, pour visualiser et synchroniser le fonctionnement de l’ensemble des usines et de la chaîne logistique en temps réel.
Entre fabrication additive, réalité virtuelle pour accompagner les personnels de production, chaine de fabrication connectée, supply chain étendue et gestion de la data industrielle, Renault embrasse la tech à bras le corps. Pour évoquer certaines des innovations majeures de ce Renault 4.0, Eric Marchiol, directeur Industrie 4.0 Renault Group, pour le côté métier, et François Lavernos, CIO de la marque Renault, pour le côté informatique, se prêtent au jeu des explications pour Solutions Numériques, tous deux pilotant collégialement la transformation via ce métavers.
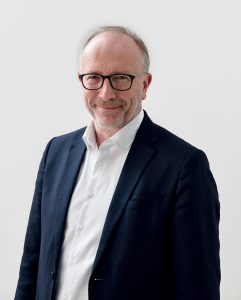
Ce métavers industriel se construit autour de quatre dimensions : la collecte des données en masse, les jumeaux numériques des process, la connexion de l’écosystème supply chain et un ensemble de technologies avancées.
Aujourd’hui, 100 % des lignes de production sont connectées (8 500 équipements), 90 % des flux d’approvisionnement sont suivis en permanence et la totalité des données supply chain sont hébergées dans le métavers du groupe, véritable replica du monde physique piloté en temps réel.
« La transformation est rendue possible aujourd’hui grâce à l’infrastructure sous-jacente, mise en place dès 2016, mais aussi avec un réseau d’innovation d’hommes et de femmes sur nos sites. C’est ce qui a permis un déploiement à l’échelle sur toutes nos usines, évitant ainsi l’effet ’’purgatoire’’ des POC. »
Eric Marchiol, CIO marque Renault
La supervision en temps réel grâce à la data
Chaque jour, c’est un milliard de sets de données qui est capté au sein des sites industriels. Le métavers offre une supervision en temps réel des opérations, ce qui permet d’agir au bon endroit et en temps réel et ainsi de réduire les coûts et d’augmenter la qualité du système de production et de la chaîne logistique. Cette supervision est aussi synonyme de prévention et d’agilité pour s’adapter aux imprévus ou aux aléas. En outre, elle est clé dans la démarche du groupe de décarbonation des sites ainsi que de la réduction de ses consommations d’énergie.
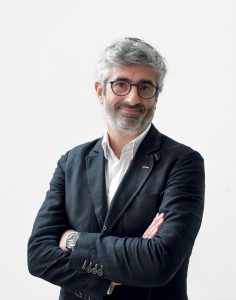
Tout commence avec « le travail de fond sur la data ». Pour récolter en masse les données de l’ensemble de ses sites industriels, Renault Group a développé en interne une solution unique de collecte et de standardisation de la data, la plateforme IDM4.0 (Industrial Data Management Platform 4.0), pour alimenter son métavers industriel. Sur cette plateforme IDM4.0, Renault a modélisé 60 procédés industriels : vissage, usinage, soudage, emboutissage, traitement thermique, process moteur électrique, etc., afin de pouvoir les reproduire.
Les data industrielles sont stockées dans le Cloud de Google et permettent de corriger ou améliorer le processus de production en temps réel. Depuis 2019, 300 alertes ont ainsi été détectées et 300 arrêts de production évités. Le constructeur a ensuite modélisé ses assets physiques en jumeaux numériques. Chaque usine disposant de son replica dans le monde virtuel.
«Après avoir standardisé, contextualisé les données, mis à l’échelle leur captation et leur stockage, nous basculons de use cases autour d’un jumeau numérique simple à un replica de notre outil industriel, à travers un métavers industriel en temps réel. »
François Lavernos, Directeur Industrie 4.0 Renault Group
Une chaîne logistique étendue
Comme les usines, la chaîne logistique dispose de son univers numérisé. Elle est pilotée, elle aussi, en temps réel par une tour de contrôle. Cette “Control Tower” est le point de convergence des métiers de la supply chain dans un espace dédié : la Control Room.
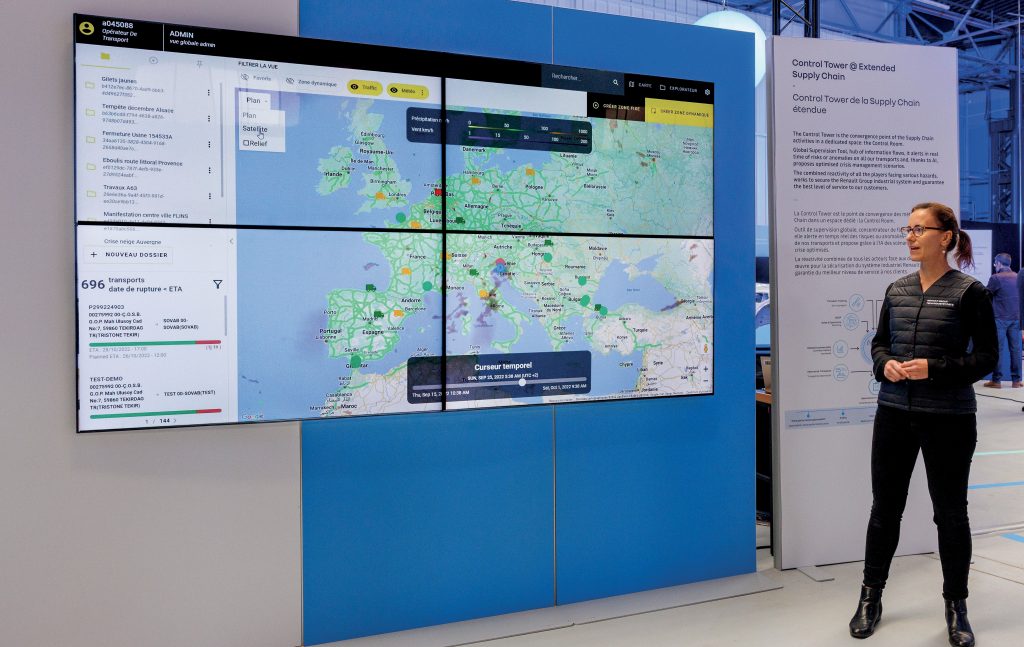
> Sur la chaîne logistique, l’ensemble des transports est tracé en temps réel pour assurer un meilleur suivi du stock pour la gestion des pièces détachées
Cet outil de supervision globale, concentrateur de flux d’informations, alerte en temps réel des risques ou anomalies sur l’ensemble des transports (voitures et camions transportant les pièces) via un dispositif de tracking, et propose des scénarios de gestion de crise optimisés grâce à l’Intelligence Artificielle. L’usage des jumeaux numériques est enrichi des données des fournisseurs, des prévisions de ventes, des informations qualités mais aussi d’informations exogènes comme la météo ou le trafic routier… ainsi que de l’Intelligence Artificielle permettant de développer des scénarios prédictifs.
Une chaine de fabrication connectée
Sur les lignes de fabrication, Renault sollicite aussi l’IA et les outils digitaux pour une mise à disposition du personnel. On retiendra notamment, via un partenariat avec Google Cloud, le développement d’une plateforme de gestion de données images qui simplifie le contrôle des véhicules par vision. Un exemple d’application est le Pokaiok wheel concept, développé en collaboration avec la société française Buwei, et qui vérifie la conformité de montage des pneumatiques et leur traçabilité réglementaire.
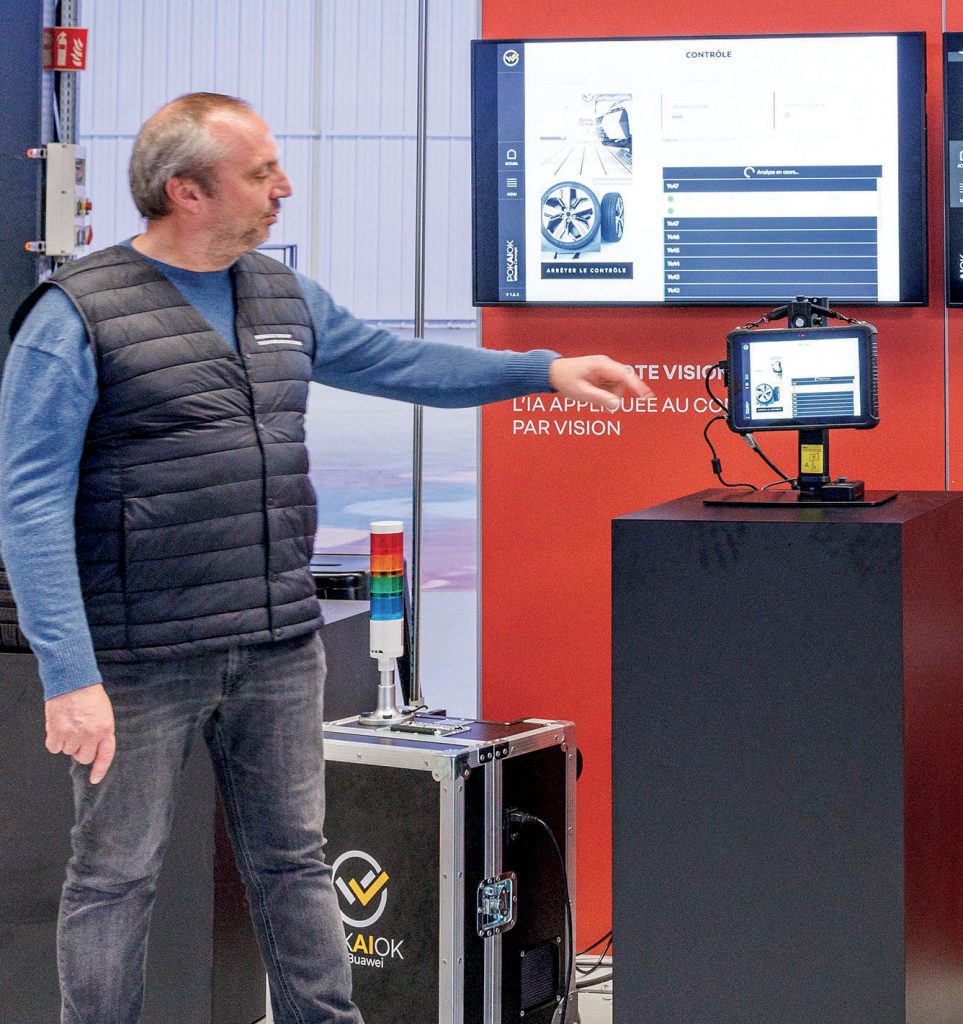
Autre solution, un contrôle déporté par vision : la fonction “Cobot”, développée en interne assure le fonctionnement autonome d’un robot couplé avec de l’IA. Avec une pince collaborative et une fonction caméra, il automatise le contrôle des pièces et facilite le travail de l’opérateur. La validation de la conformité des pièces peut ainsi se faire sans manipulation. Dernier exemple : les opérateurs sont équipés d’une tablette Digital Work Station (DWS) apportant toutes les informations utiles pour tenir le poste, par exemple, les véhicules en cours de production et à venir, et permet de formuler des requêtes en temps réel au chef d’équipe. Ce dernier est lui-même équipé d’une tablette (CHUET) pour visualiser tous les évènements en temps réel.
Les bénéfices financiers du métavers de Renault
D’ici à 2025, Renault chiffre :
- 320 M€ d’économies diverses
- 260 M€ d’économies sur les stocks
- réduction de 60 % du délai de livraison des véhicules
- réduction de 50 % de l’empreinte carbone de la fabrication des véhivules
- contribution à la réduction de 60 % des coûts de garantie visée par le groupe.
- Engagé dans l’Industrie 4.0 depuis 2016, le digital a déjà permis de réaliser un gain de 780 M€ d’économie.